We never stop innovating
Keeping pace with the most competitive industries and their drive for new products that last longer, perform better, and cost less requires continuous innovation. At Fisher Barton, we never stop inventing, improving, and innovating with new materials solutions that perform better. We call it Metallurgy Mastered. It’s more than just a theme; it’s a methodology unique to Fisher Barton. Fisher Barton’s search for new solutions benefits from the synergies between our divisions, combined with over 50 years of metallurgy expertise and the powerful technology R&D capabilities made available at our own Fisher Barton Technology Center.
Fisher Barton Technology Center
The Fisher Barton Technology Center puts us at the forefront of the search for new materials solutions. Visit the Fisher Barton Technology Center on any given day and you’ll find our team of R&D engineers using a full array of advanced analytical tools to evaluate the performance characteristics of everything from tool steels to titanium, high carbon steels to carbides and ceramics, as well as the application of advanced new coatings to enhance corrosion and wear resistance, thermal protection and dielectric strength. It’s here that dozens of patented Fisher Barton innovations were born, products like MARBAIN®, LaserEdge®, FUSIONBond® and many others that are now ‘household’ names in the industries they benefit.
Learn MoreCoating Methods
Thermal spray is a group of processes that use combustion of gases or electrical energy to melt feedstock material in wire, powder, or rod form. The melted material is atomized and propelled to a prepared surface where the material immediately freezes and builds up to create a coating. The processes are extremely versatile and able to create coatings out of almost an endless number of materials. The technology is used in several industries to provide engineered coated surfaces for improving the components performance.
Learn MoreHeat Treating
Heat treat is an age-old process that improves strength, hardness, toughness, ductility, and corrosion resistance in metals. At Fisher Barton, it’s both science and art. It’s here that metallurgy is mastered through the application of worldclass heat treatment resources to transform metal into products that last longer and perform better.
Learn MoreMachining
Through a controlled material removal process metal is cut into a desired final shape and size.
CNC Machining
Large Capacity Vertical Turning – Accurate Specialties, Inc. provides precision machining services using our state-of-the-art Fives Giddings & Lewis VTC (Vertical Turning Center) 2500. This machine tool is powerful, versatile, and highly accurate, with a large-capacity work envelope (2.5m/8ft x 1m/3.25ft).
Close Tolerance Machining
Fisher Barton produces high-quality components through our CNC machining services. We specialize in precision close tolerance machining to create complex components that adhere to tight design parameters. Our close tolerance machining capabilities allow us to produce high-performance specialty goods for all major industries. Learn more about the benefits of close tolerance machining, the applications of this service, and how Fisher Barton can partner with you on your next project.
Learn MoreCNC Precision Machining
CNC precision machining utilizes Computer Numerical Control (CNC) equipment to cut, mill, turn, and electrically discharge large materials. This precision machining technology can meet the exact specifications of an application, producing parts with strict tolerances that adhere to the highest standards.
Learn More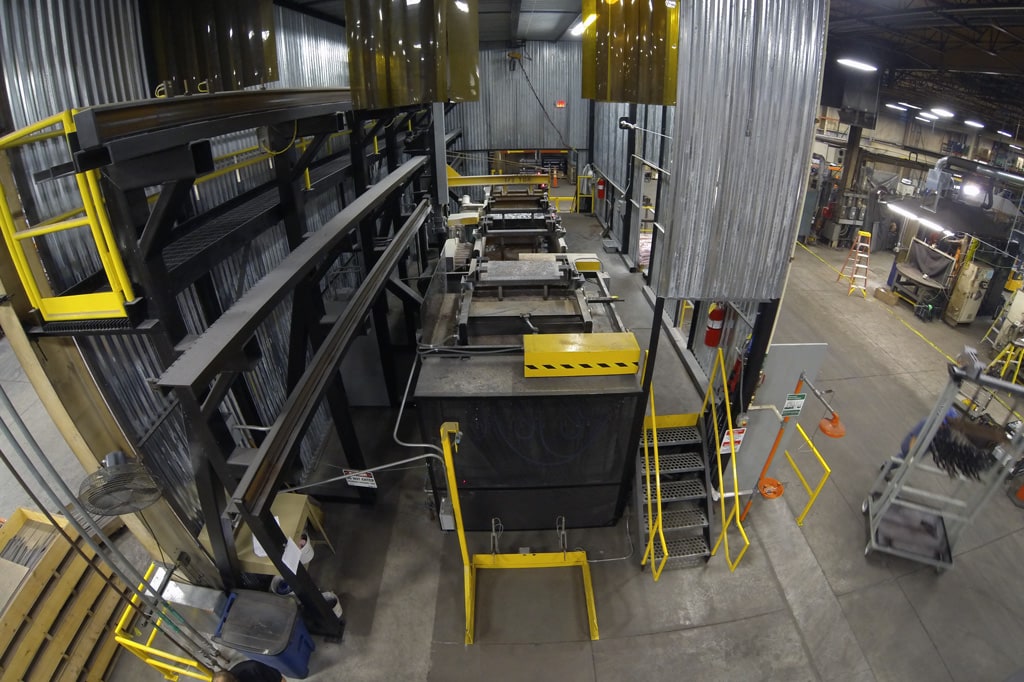
Stamping Bending & Forming
Ability to stamp, and form metals up to 0.375″ thick and up to 23″ wide sheet.
- Small to Medium Press
- Medium to Large Press (1,000 ton capacity)
- Light to Medium Tonnage (Up to 600 ton)
- Medium to High Tonnage (600 tons to 1000 ton)
- Hydraulic Press
- Press Brake
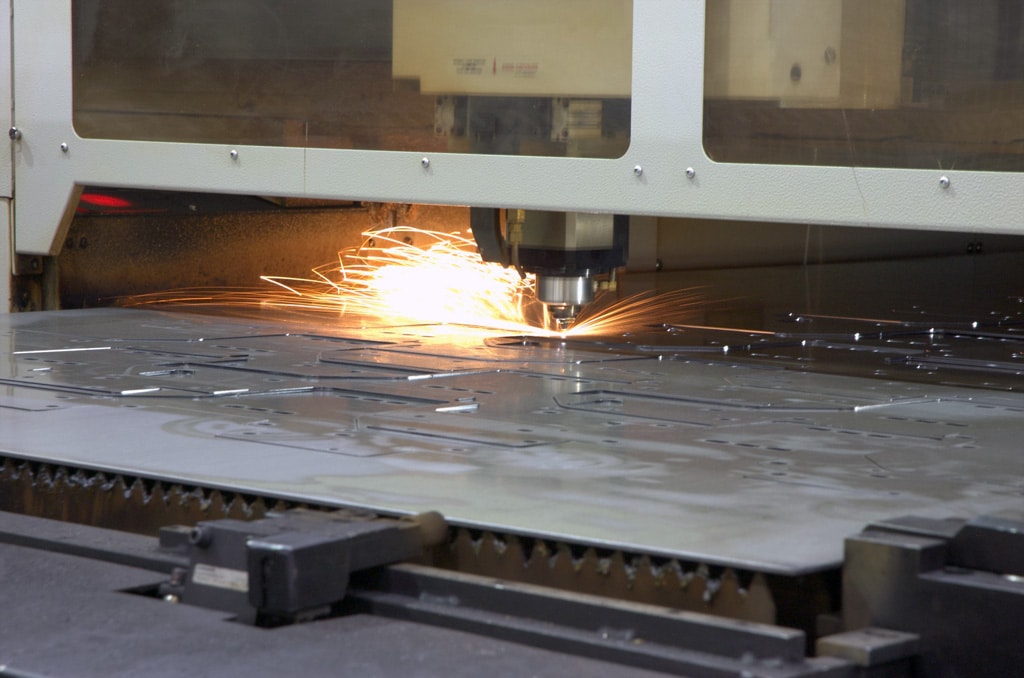
Cutting
Ability to cut metal to 0.500″ thick up to 60″ X 120″ sheet.
- Laser – 2000-3500 Watt
- Laser – 4000 Higher Watt
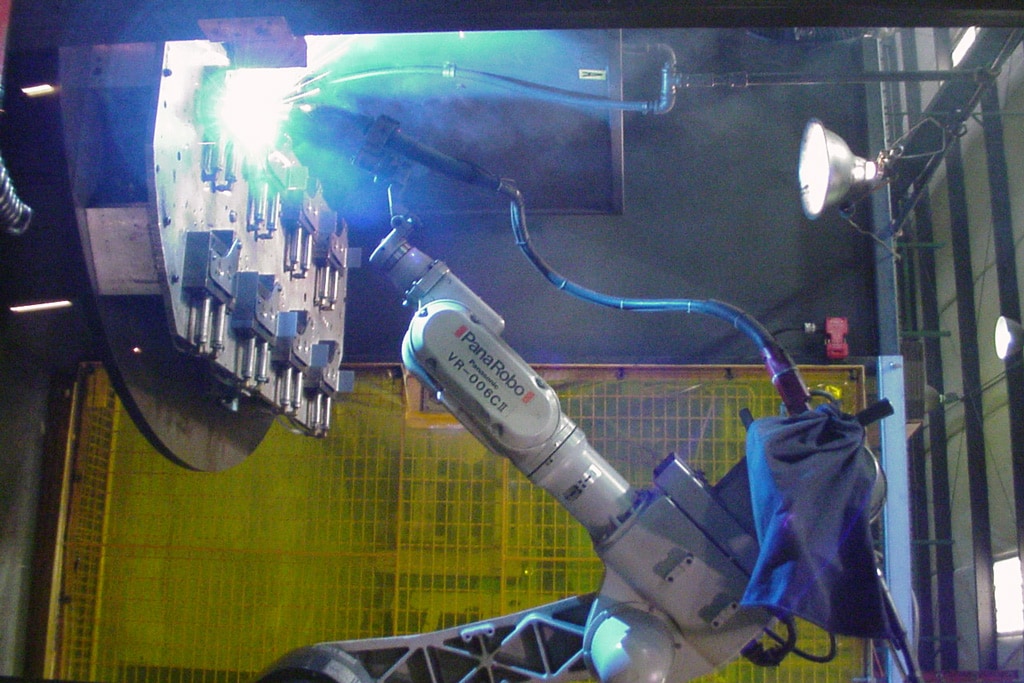
Welding
Fabrication process of joining metals together to create fusion either manually or robotically.
- Light gage (< 6mm) Medium gage (6mm-12mm) Heavy gage (> 12mm)
- MIG Welding – Metal Inert Gas Welding, Low oxidation, high welding speeds – iron based coatings and low carbon steel fabrications.
- TIG Welding -Tungsten-electrode inert gas welding, low oxidation, high welding speeds. Primarily used for aluminum, magnesium, copper, and stainless steel.
- Robotic Welding – Ensure reliable consistent weld at high speed. Additive welding for wear resistance and welding for fabrication
Product Development and Prototyping
Fisher Barton’s Product Development Team is dedicated to bringing new products into production. You already know Fisher Barton has a deep bench of metallurgical expertise. These experts are ready to partner with you to bring your ideas to prototype and ultimately production.
We use leading-edge scanning applications to create full 3D models of your component. Scans can be aligned for geometric dimensioning and tolerancing (GD&T) specs and use a CAD model for reference. Even complex measurements can be done quickly and accurately. Examples: cylindricity, hole position, line profiles, and runout.
Colormaps
Colormaps can be created to help visualize deviations from the cad model using a heat map. They are most useful for easily summarizing results for quick reports. Individual points can be selected for exact numbers.
Failure Analysis
Colormaps can also be used for accurately visualizing where a component is out of specification. This makes error analysis quick and easy as out-of-spec locations can be immediately identified with accurate numbers. The example above is a part with a low offset.
Additional Capabilities
Tool Design – In house tool and die design and manufacturing capabilities.
Tool Making – In house tool making capabilities
Thermal Powders – Variety of powders used for Thermal spray process resulting in improved wear and corrosion resistance characteristics.
Shot Blasting – Remove any rust scale and corrosion providing an ideal bonding area and work harden the surface.
Assembly – In house manufacturing to full assembly.
Packaging – Packaging and kitting to customer requirements.